Driving surface finish innovation with multifunctional additives
When selecting additives, the coatings industry strives to balance aesthetic appeal, durability, and cost efficiency.
Traditional silica-based matting agents have been used to achieve matte finishes, but these solutions can introduce several challenges. In a recent survey* conducted by Coatings World and Honeywell, respondents were asked to list the challenges they are facing with their current matting agents—viscosity issues with silica-based additives, poor scratch resistance, and difficulty achieving a balance between matte finish and durability ranked as the top challenges, besides cost.
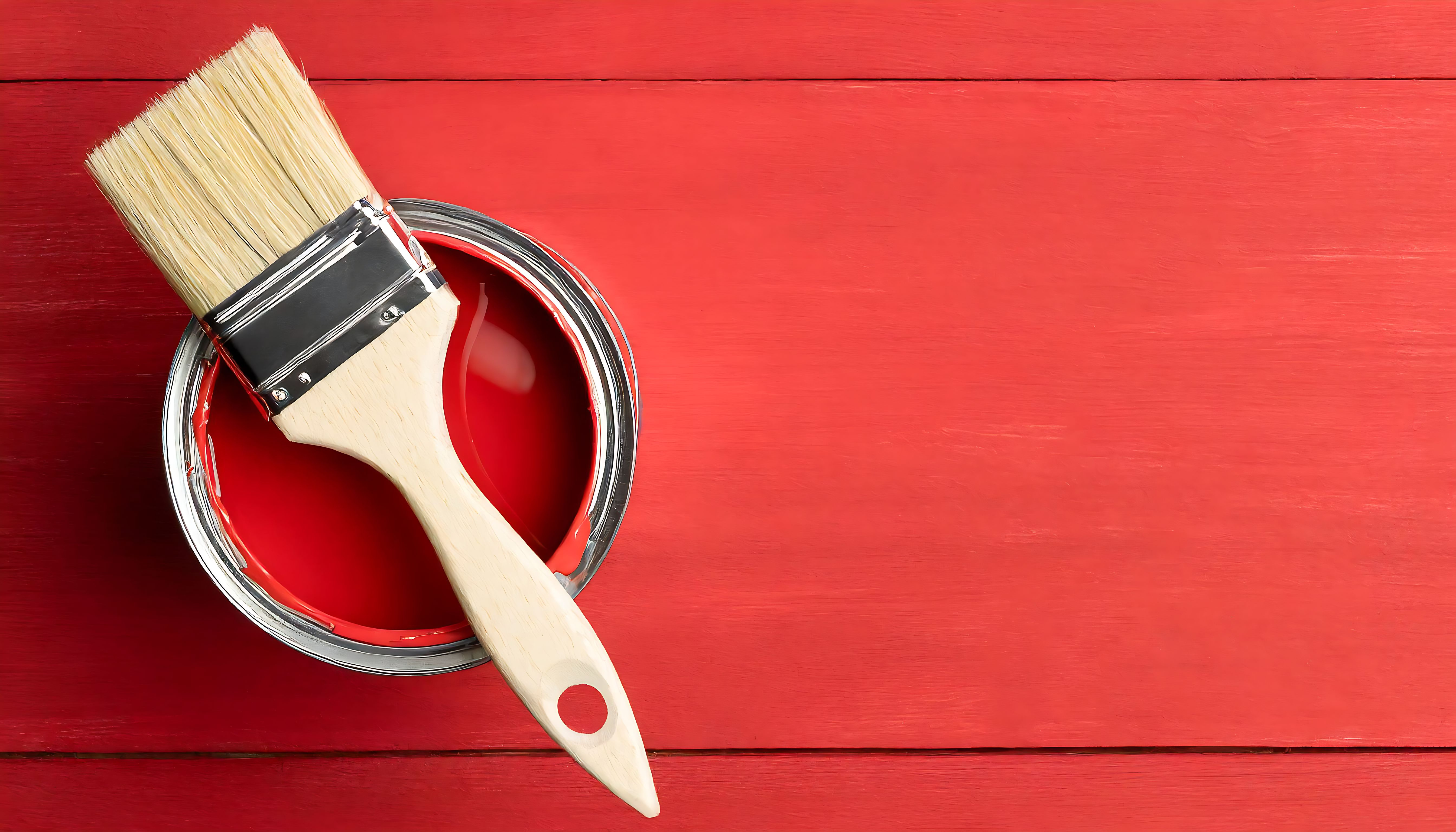
For more information, please contact:
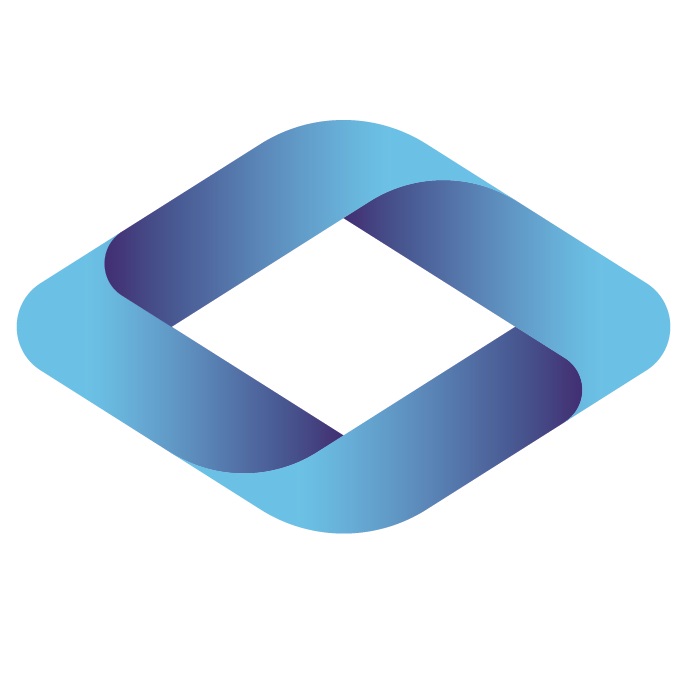
In the survey, when asked to list their opinion regarding the same, respondents listed their expectations as below: When choosing an additive, a formulator has several key criteria to consider. “Achieving the desired performance characteristics and compatibility or ease of incorporation with the paint formulation are two of the main considerations. Additives finetune the paint properties such as durability and resistance to environmental factors,” said Rajesh Wadhwani, Senior Offering Manager Specialty Additives at Honeywell.
Formulators should consider the type of paint and coating they are developing. The ideal additive will depend on whether the paint is water-based or oil-based. “That’s why it becomes a key part of choosing the right kind of additive in the formulation,” said Wadhwani. “Desired color and appearance can affect the finished gloss level and color intensity of the paint, thereby impacting the final aesthetics of the coating. Additives can enhance the overall application process by making the paint easier to mix, apply, and clean, ultimately improving its ease of use.
Lastly, cost-effective additives can positively contribute to the overall cost of the formulation. Selecting the additive that offers the best pricing and performance balance is crucial.”
Matting agents and their role in paint formulation
Matting agents are an important addition when formulating paint. They are critical in controlling gloss levels in architectural and wood coatings applications. So why is gloss important?
“Gloss is the amount of light reflected directly from a surface that can affect the aesthetics and functional attributes of a coating,” noted Wadhwani. “High gloss finish might be desirable for certain applications for the reflectiveness and ease of cleaning, but in other scenarios, a matte finish is preferred for its non-reflective, sophisticated interference that hides surface imperfections.”
The light source and the receiver are the key criteria in defining gloss. “That means when light hits the coated surface, it either reflects or scatters depending on the coating,” Wadhwani explained. “Finished matting agents are incorporated into a formulation to scatter more light and reduce the reflection. This scattering diffuses the light, diminishing the gloss to achieve the desired level of matteness. The importance of matting is not just aesthetics; it also affects how we perceive the quality and durability of the paint.”
Adding matting agents to the paint formulation and tailoring the final product to meet the requirements of finish and durability makes it suitable for various consumer preferences, particularly for architectural and wood coatings.
Multi-functional additives versus traditional additives
A multi-functional additive is an ideal alternative to traditional additives. Multi-functional additives can help the formulator achieve the desired amount of gloss reduction/matt finish, improve surface properties, and boost the overall performance of the paint.
Honeywell Specialty Additives embarked on a project to develop a product with a lower gloss finish. “Five years ago, here in the U.S., many coatings that were traditionally only produced in a high gloss finish. But now, customers are demanding low gloss finishes with the same level of durability. However, they were not achieving it, said Mike Jablon, Lead Scientist and R&D Manager at Honeywell.
In the survey, close to 40% of the respondents indicated using multi-functional additives as one of the ways to address the challenges they face with their current matting agents. “We explored the combination of traditional matting agents and our micronized polymeric materials to improve overall surface property performance, such as abrasion, burnish, and scratch resistance while retaining the matting effect provided by conventional matting agents,” said Jablon. “However, we recognized the need for a single additive to deliver both properties effectively. This led us back to the drawing board, where we spent a couple of years designing a unique polymer with optimized particle size and distribution to deliver exceptional matting efficiency and enhanced surface property performance. Once we developed NduroMatt™ we rigorously tested it across various inks and coatings formulations to confirm its effectiveness.”
One of the reasons these materials work in the way they do and provide excellent surface property performance and improved stain resistance is related to the oil absorption number. “Silicas are designed with high porosity to be effective filtration aids with high absorbency, so they’re going to tend to absorb more staining than our materials would,” said Jablon. Jablon also stated: “NduroMatt™ materials are non-porous polymeric particles and do not behave in that manner.”
Initially, Honeywell launched three products: NduroMatt™ 100, 200, and 300. “When we looked at these materials, we found that using materials of 20-micron average particle size for a coating that was applied 4 mils (100 microns) wet and dried to two mils (50 microns) dry gave us the best balance of gloss reduction and surface properties. Once we introduced these materials, our wood coating and ink customers requested we make these materials smaller”. Honeywell developed a method to develop smaller sizes, so they are now offered in 6,12 and 20-micron versions.
“There are now nine commercially available products,” said Jablon. “The difference between these materials is as follows: NduroMatt™ 100 is a very hard, crystalline, polyethylene material targeted for solvent-based systems. NduroMatt™ 200 is a harder, even more crystalline polyethylene material if you don’t quite get the surface properties you need out of the 100, which is the baseline product. NduroMatt™ 300 is an oxidized version of the 200 to make it more hydrophilic and, thereby, easier to disperse into water-based systems.
The family of NduroMatt™polymer-based, multi-functional additives delivers durability and efficient, easy-to-use matting technology that meets the demands of architectural, industrial, and specialty coatings. Recognizing the need for innovation, Honeywell developed NduroMatt™polymer-based additives designed to deliver the benefits of traditional matting agents while addressing their shortcomings.
“NduroMatt™ redefines what’s possible for surface finishes,” noted Jablon. “Its unique polymer chemistry ensures efficient gloss reduction while enhancing durability and surface properties.”
“Our goal was to flip the value proposition. Every additional pound of NduroMatt™ added to a formulation enhances surface performance, unlike traditional matting agents that compromise the coating’s integrity. Honeywell’s dedication to innovation meets evolving market demands and enhances the quality and performance of coatings, ensuring that both aesthetic appeal and functional attributes are achieved simultaneously,” concludes Jablon.
*Coatings World and Honeywell conducted the survey in November 2024 with a sample size of 147 respondents from 30 countries worldwide. The respondents include Formulators, Research Scientists, Chemists, Product Development Managers and Business Leaders.
Distributed in:
Austria, Bulgaria, Croatia, the Czech Republic, Denmark, Finland, France, Germany, Hungary, Norway, Poland, Romania, Serbia, Slovakia, Slovenia, Sweden and Turkey.
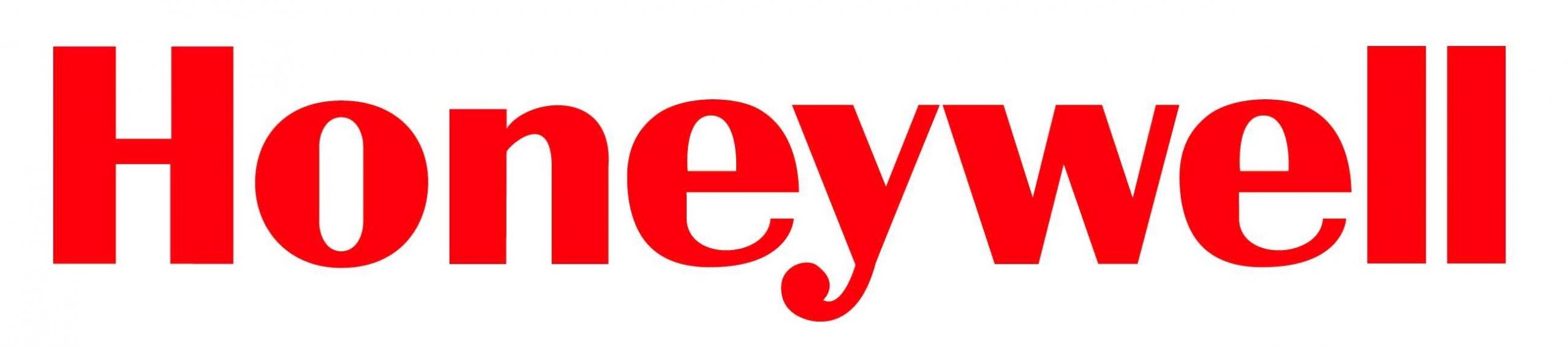
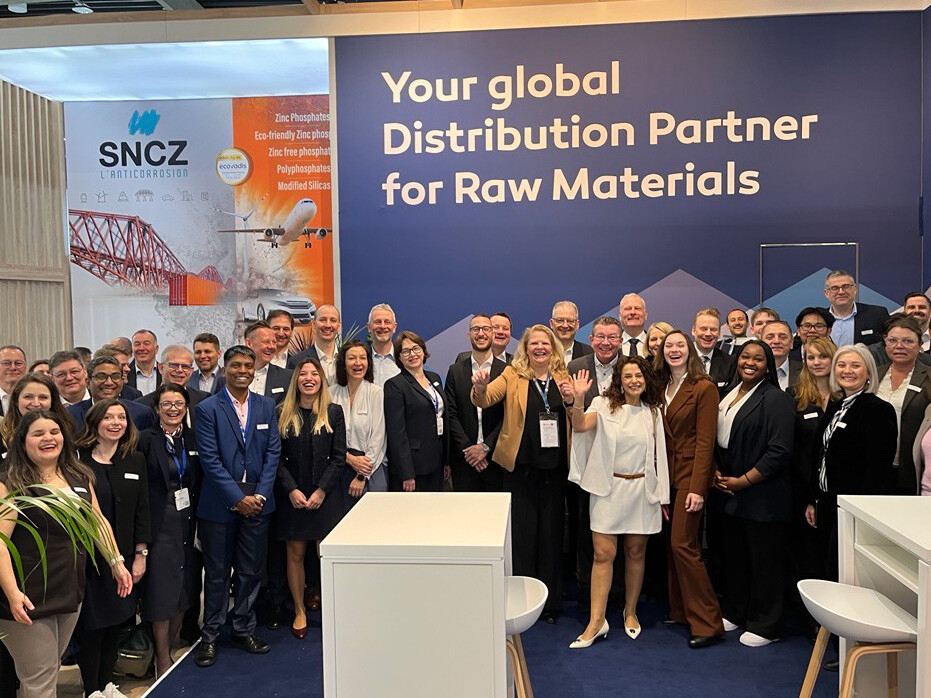
Nordmann at the European Coatings Show 2025: A look back
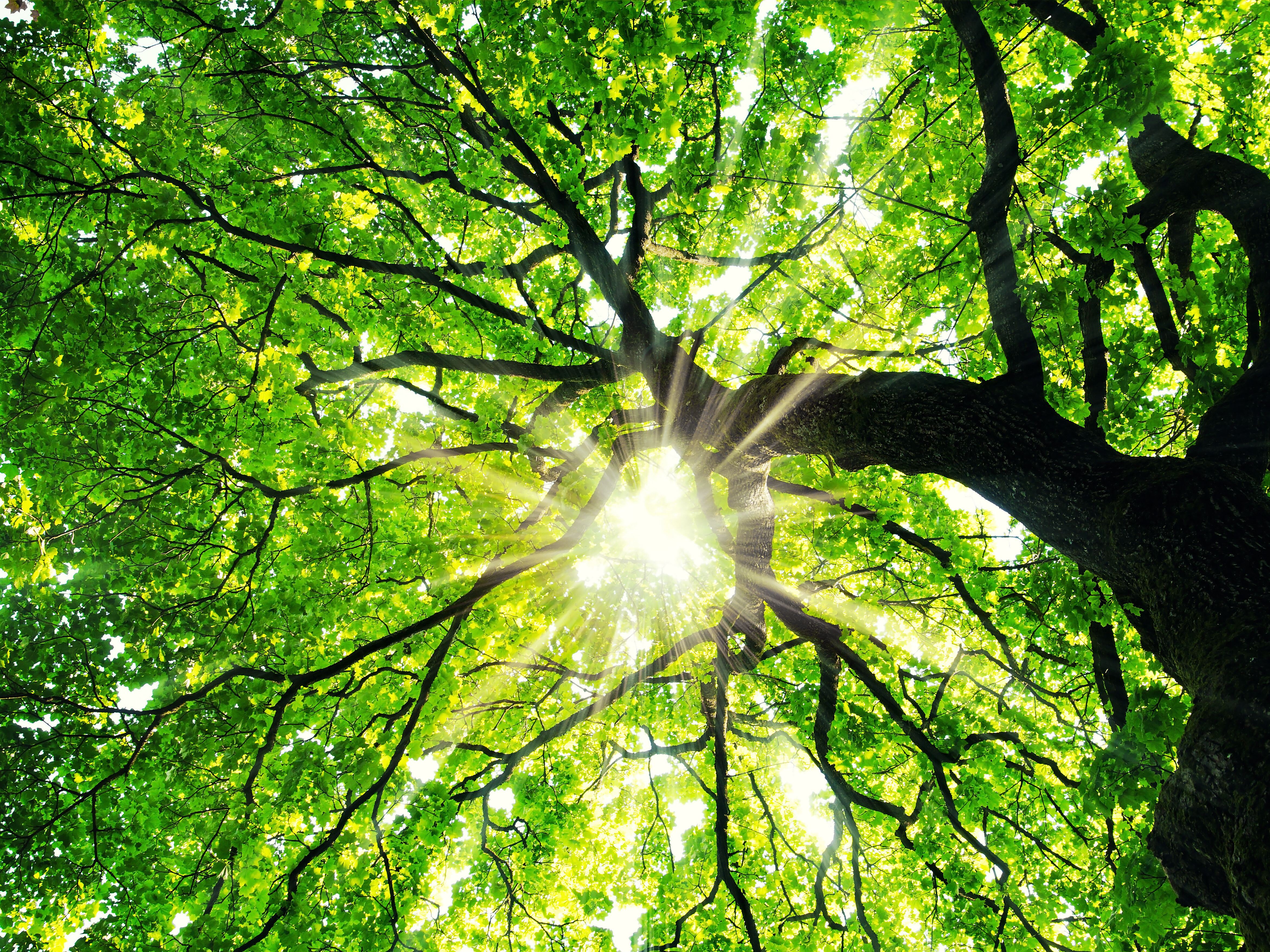
EU SVHC regulations: Challenges and solutions for light stabilizers
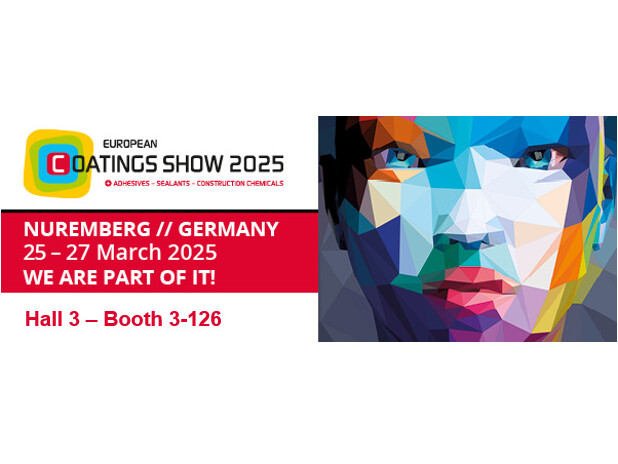